5 Essential Bearings in Transmission Systems Must Check
Bearings are crucial in mechanical systems, playing a key role in things like transmissions. They support rotating parts, cut down on friction, and help ensure that power transfers smoothly. Whether in car gearboxes or heavy-duty industrial machines, bearings are vital for reliable performance. In this article, we’ll explore bearings in depth—from how they’re designed and the materials used to how they handle loads and the latest tech advancements. Our goal is to provide useful insights for both engineers and hobbyists, blending theory with practical advice.
Top 5 Bearings and Their Applications
Bearings play a critical role in mechanical systems by reducing friction and supporting loads, ensuring smooth rotational or linear motion. There are different types of bearings in transmission system, each designed for specific applications and load conditions. In this article, we will focus on five common types of bearings: ball bearings, cylindrical bearings, taper roller bearings, needle bearings, and thrust bearings.
1. Ball Bearing
Application: Ball bearings are one of the most widely used bearings, known for their ability to handle both radial and light axial loads. They are commonly found in household appliances, electric motors, and automotive transmissions.
Load Handling: Ball bearings are primarily designed to support radial loads (loads perpendicular to the shaft) but can also take on light axial loads (loads parallel to the shaft). The rolling element, which is a ball, makes point contact with the raceways, reducing friction but limiting the capacity for heavy axial loads.

2. Cylindrical Roller Bearing
Application: Cylindrical roller bearings are used in applications that involve heavy radial loads, such as in gearboxes, electric motors, and wind turbines. They are ideal for supporting high-speed applications.
Load Handling: These bearings mainly handle radial loads due to the large contact area between the cylindrical rollers and raceways. However, cylindrical bearings are not suitable for significant axial loads unless specially designed with flanges on the inner or outer raceways.

3. Taper Roller Bearing
Application: Taper roller bearings are widely used in automotive axle systems, machine tool spindles, and gear reducers. They are ideal for applications requiring high radial and axial load capacity, such as in wheel hubs of vehicles.
Load Handling: These bearings can handle combined radial and axial loads. The conical shape of the rollers allows for efficient load distribution along the axis, making them excellent at handling axial loads in one direction, along with high radial loads. If axial loads in both directions are required, paired sets of taper roller bearings can be used.
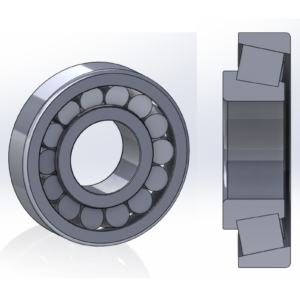
4. Needle Bearing
Application: Needle bearings, with their thin, elongated rollers, are found in compact applications where space is limited, such as in automotive transmissions, jet engines, and two-stroke engines.
Load Handling: Needle bearings primarily support radial loads. The small diameter of the needle rollers allows for higher load-carrying capacity in a small footprint. However, they are not designed to take on significant axial loads unless used in conjunction with another type of bearing, such as thrust bearings.
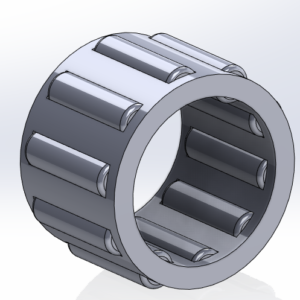
5. Thrust Bearing
Application: Thrust bearings are designed to support axial loads and are often found in automotive clutches, propeller shafts, and rotary tables in machine tools.
Load Handling: As the name suggests, thrust bearings are specialized for taking axial loads (loads parallel to the shaft). They do not handle radial loads well and are typically used in applications where the main forces are axial. Thrust bearings can be in the form of ball or roller designs, depending on the load capacity required.

Bearing Designation and Nomenclature (Bearing Size)
Understanding bearing designations is critical for selecting the right bearings in transmission system. Most bearings follow the ISO 15 standard, which defines their dimensional series. A typical designation, such as 6306C3, consists of several components:
- Type Code (First digit): This indicates the bearing type. For example, 6 signifies a deep groove ball bearing.
- Dimension Series (Next two digits): These indicate the bearing’s outer diameter and width in proportion to its bore size.
- Bore Size: The last digits indicate the bore size, which is typically five times the value (e.g., ’06’ represents a 30 mm bore).
- Clearance Suffix (C3, C4): The suffix provides additional information about internal clearance, which is crucial for performance under different temperature and load conditions.
Breakdown Example:
- 6206ZZC3:
- 6: Deep groove ball bearing.
- 2: Medium series.
- 06: 30 mm bore.
- ZZ: Shielded on both sides.
- C3: Greater internal clearance than standard.
This system is standardized globally, making it easy to identify and select bearings with precise attributes for specific transmission applications.
Limiting Speed: Critical for High-Performance Transmissions
Limiting speed refers to the maximum rotational speed at which a bearing can operate without generating excessive heat, which would reduce lubrication efficiency or cause wear. The limiting speed of a bearing is affected by factors such as:
- Bearing type (e.g., ball or roller bearings).
- Lubrication type (grease or oil).
- Bearing size (smaller bearings generally allow for higher speeds).
- Environmental factors (temperature, load, and contamination).
High-speed applications, such as automotive or aerospace transmissions, often require ceramic ball bearings in transmission because they can operate at speeds up to 50% higher than traditional steel bearings. To ensure safe operation within the limiting speed, consult the manufacturer’s catalog, which provides speed ratings for specific lubrication and loading conditions.
Types of Fits in Bearings
The type of fit between the bearing and its housing or shaft plays a pivotal role in the performance and longevity of the bearing system. Selecting the wrong fit can lead to slippage, misalignment, or excessive stress.
Types of Fits:
- Interference Fit (Press Fit): The bearing is slightly larger than the shaft or housing, creating a secure fit when pressed into place. Common in high-load transmission systems where zero relative motion between the shaft and bearing is essential.
- Application: Automotive gearbox shafts.
- Transition Fit: A balanced fit between interference and clearance, offering slight mobility. Typically used where some adjustment is necessary but excessive movement could be detrimental.
- Application: Moderate-load applications in machinery.
- Clearance Fit: The bearing is slightly smaller than the shaft or housing, allowing for easy installation and removal. Common in systems that experience frequent temperature changes or require assembly and disassembly.
- Application: Light-load assemblies, such as electric motor housings.
For transmission systems, engineers must carefully select fits based on operational speed, load, temperature, and precision requirements. learn more on Fit, click here
Bearing Materials: Strength and Durability
The choice of material affects a bearing’s load capacity, wear resistance, and suitability for specific environments.
- High-Carbon Chromium Steel (52100): The most common material used for bearings due to its high hardness and wear resistance. This steel provides the necessary strength for heavy-duty applications like automotive and industrial transmissions.
- Stainless Steel (440C): Offers excellent corrosion resistance and is suitable for applications where exposure to moisture or chemicals is expected.
- Ceramics (Si3N4 – Silicon Nitride): A premium choice for high-speed or high-temperature environments. Ceramic bearings have a lower coefficient of friction and are significantly lighter than steel bearings, making them ideal for high-performance automotive or aerospace gearboxes.
- Polymer Bearings: For low-load applications, polymer bearings offer the advantage of being self-lubricating and resistant to corrosive environments. These are common in low-speed electric motors or equipment exposed to chemicals.
Material choice directly impacts the bearing’s performance in specific environments and should align with the operational demands of the bearings in transmission system.
Dynamic and Static Load Ratings
Bearings are subjected to varying loads in transmission systems, making load ratings an essential consideration for longevity and reliability.
- Dynamic Load Rating (C): Defines the bearing’s capacity to handle loads during rotation. This is critical in high-speed applications where the load constantly fluctuates, such as in automotive transmissions. The dynamic load rating is used to estimate the bearing life using the L10 life formula, which predicts that 90% of bearings will last for the calculated time under a given load.
- Static Load Rating (C0): Specifies the load that a bearing can withstand when stationary without causing permanent deformation. Static loads are crucial in scenarios like idle heavy machinery or when a transmission system is subjected to shock loads during starts and stops.
To ensure optimal performance, bearings must be chosen based on the load conditions they will encounter during operation.
Axial and Radial Clearance
Bearings are designed to handle both axial (thrust) and radial loads, and the internal clearance of the bearing significantly influences its operational performance.
- Radial Clearance: This is the clearance perpendicular to the shaft and plays a role in the bearing’s ability to accommodate radial loads and thermal expansion. For most transmission systems, standard clearances (C0) or increased clearances (C3) are used based on the load and temperature conditions.
- Axial Clearance: This refers to the internal clearance along the shaft axis. High axial clearance may be required in systems with significant shaft elongation due to thermal effects, while tighter axial clearances provide greater precision in systems with minimal axial movement.
Bearings in transmission systems should be selected with the appropriate clearance class (C2, C3, etc.), depending on operational requirements. For instance, a gearbox subjected to extreme temperature variations would benefit from C3 or C4 clearance classes, which allow for more thermal expansion without compromising performance.
Bearing Tolerance and Precision
Bearings are manufactured to stringent tolerances to ensure precision and smooth operation. ISO 492 defines tolerance classes, with higher precision classes (P5, P4, etc.) used in applications where minimal deviation is allowed. In transmission systems, the tolerance class should be chosen based on the desired level of smoothness and the potential for misalignment.
- Higher precision bearings (P5 or P4): Used in high-speed transmissions, where any deviation in dimensions can lead to excessive vibration or wear.
- Standard precision bearings (P6 or P0): Adequate for most industrial and automotive transmission applications.
Bearings with tighter tolerances reduce vibration and ensure optimal load distribution across the bearing’s contact surfaces, enhancing both performance and life.
Operating Radial Clearance and Its Impact on Bearing Life
Operating radial clearance refers to the effective clearance of a bearings in transmission during operation, considering factors such as thermal expansion and load. Improper radial clearance can lead to a host of issues, including:
- Too Little Clearance: Results in excessive heat buildup, friction, and wear. This scenario is common in high-speed transmissions without proper lubrication or cooling.
- Too Much Clearance: Leads to bearing instability, noise, and vibration, particularly in applications requiring precise alignment, such as high-performance automotive gearboxes.
Choosing the correct operating clearance ensures that the bearing functions optimally under both load and thermal conditions. Engineers should adjust for factors such as expansion coefficients when selecting a bearings in transmission for a specific operating environment.
Bearing Life Calculation
The L10 life or basic rating life of a bearing is calculated using the dynamic load rating (C) and the applied load (P). The formula is:
Where:
- L10 is the bearing life in revolutions,
- C is the dynamic load rating,
- P is the equivalent dynamic load acting on the bearing.
You can also use our Online Bearing Life Calculator
This calculation assumes the load is constant and acts consistently over time. In real-world applications, load variability can affect the bearing life. To estimate life more accurately, engineers may use adjusted life factors to account for variable loads, lubrication conditions, and contamination levels.
Failure Modes of Bearings in Tranmission
Bearing failure can drastically reduce the efficiency of transmission systems, often leading to costly downtime. Understanding the common failure modes helps in preventing premature failure:
- Fatigue Failure: Caused by repeated stress cycles that exceed the bearing’s fatigue limit. Over time, the raceways and rolling elements develop cracks, leading to material spalling.
- Wear Failure: Results from inadequate lubrication or contamination. As friction increases due to insufficient lubrication, the surfaces degrade, causing material loss and eventually failure.
- Corrosion: Bearings exposed to moisture or chemical contamination can experience corrosion, which reduces load-bearing capacity and causes uneven wear.
- Misalignment: If the shaft and bearing are not perfectly aligned, uneven load distribution occurs, leading to accelerated wear and eventual failure.
- Ball Bearing Truncation: Ball bearing truncation refers to a condition where the rolling elements (balls) do not fully conform to the intended geometry, resulting in partial contact between the balls and raceways. This uneven load distribution leads to localized stress, causing premature wear and increased friction, potentially leading to bearing failure. Ensuring proper design, load capacity, and installation can help prevent truncation and extend bearing life.
Regular maintenance, proper lubrication, and precise alignment during
Conclusion
Different types of bearings are designed to handle specific types of loads—whether radial, axial, or a combination of both. Ball bearings offer versatility for light axial and radial loads, while cylindrical and needle bearings are optimized for high radial loads. Taper roller bearings handle combined loads effectively, and thrust bearings are essential when dealing exclusively with axial loads. Selecting the right bearing for your application ensures smooth operation and long-term reliability.
For more information read here also,
Thank you!